ग्राइन्डिङ डिस्कहरूले विभिन्न उद्योगहरूमा महत्त्वपूर्ण भूमिका खेल्छन्, जसले सामग्रीहरूको आकार र परिष्करणलाई सहज बनाउँछ। यद्यपि, कुनै पनि अन्य उपकरण जस्तै, तिनीहरू तिनीहरूको दक्षता र कार्यसम्पादनमा बाधा पुर्याउन सक्ने समस्याहरूबाट मुक्त छैनन्। यस लेखमा, हामी सामान्य ग्राइन्डिङ डिस्क समस्याहरूको खोजी गर्नेछौं, तिनीहरूका मूल कारणहरू अन्वेषण गर्नेछौं, र निर्बाध कार्यप्रवाहको लागि प्रभावकारी समाधानहरू प्रदान गर्नेछौं।
परिचय
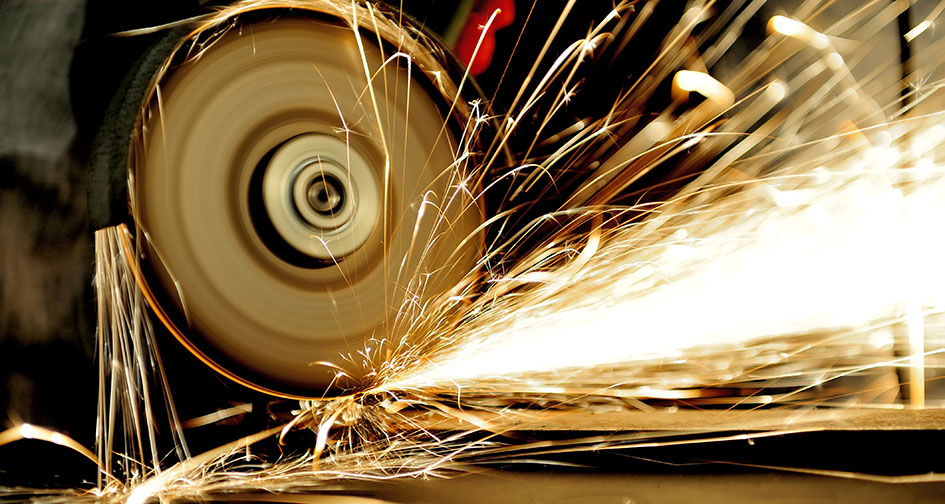
ग्राइन्डिङ डिस्कहरूले विभिन्न उद्योगहरूमा आधारभूत भूमिका खेल्छन्, सामग्री हटाउने, आकार दिने र परिष्करण प्रक्रियाहरूको लागि आवश्यक उपकरणको रूपमा काम गर्छन्। तिनीहरूको परिभाषा, उद्योगहरूमा महत्त्व, र सामना गर्ने सामान्य समस्याहरू बुझ्नु तिनीहरूको प्रयोगलाई अनुकूलन गर्न र कुशल सञ्चालन सुनिश्चित गर्न महत्त्वपूर्ण छ।
A. ग्राइन्डिङ डिस्कको परिभाषा
ग्राइन्डिङ डिस्कहरू सामग्रीको सतहहरू काट्न, पिस्न वा पालिस गर्न मेसिनिङ प्रक्रियाहरूमा प्रयोग गरिने घर्षण उपकरणहरू हुन्। यी डिस्कहरूमा सामान्यतया ब्याकिङ सामग्रीमा बाँधिएका घर्षण कणहरू हुन्छन्, जसले घुम्ने उपकरण सिर्जना गर्दछ जसले अतिरिक्त सामग्री हटाउन, चिल्लो सतहहरू हटाउन वा किनारहरू तिखार्न सक्छ। तिनीहरू विभिन्न आकार र आकारहरूमा आउँछन्, प्रत्येक विशिष्ट अनुप्रयोगहरूको लागि डिजाइन गरिएको हो।
ख. विभिन्न उद्योगहरूमा महत्व
धातु उद्योग:
धातु निर्माण र निर्माणमा, ग्राइन्डिङ डिस्कहरू धातुको सतहहरूलाई आकार दिन, डिबरिङ गर्न र परिष्करण गर्न महत्त्वपूर्ण हुन्छन्। तिनीहरू सामान्यतया कोण ग्राइन्डरहरूसँग सटीक आयाम र सतहको गुणस्तर प्राप्त गर्न प्रयोग गरिन्छ।
निर्माण उद्योग:
निर्माण पेशेवरहरू कंक्रीटको सतह तयारी गर्ने, कुनै न कुनै किनाराहरू चिल्लो पार्ने, र ढुङ्गा र कंक्रीट जस्ता सामग्रीहरूमा भएका त्रुटिहरू हटाउने जस्ता कार्यहरूको लागि ग्राइन्डिङ डिस्कहरूमा भर पर्छन्।
अटोमोटिभ उद्योग:
अटोमोटिभ क्षेत्रमा ग्राइन्डिङ डिस्कहरू उपकरणहरू तिखार्नेदेखि धातुका कम्पोनेन्टहरूलाई आकार दिने र परिष्करण गर्ने जस्ता कार्यहरूको लागि आवश्यक छन्। तिनीहरूले अटोमोटिभ पार्टपुर्जाको शुद्धता र गुणस्तरमा योगदान पुर्याउँछन्।
काठको काम गर्ने उद्योग:
काठका कामदारहरूले काठको सतहहरूलाई आकार दिन र चिल्लो बनाउन ग्राइन्डिङ डिस्कहरू प्रयोग गर्छन्। यी डिस्कहरू अतिरिक्त सामग्री हटाउन, आकारहरू परिष्कृत गर्न र थप परिष्करणको लागि काठ तयार गर्न प्रभावकारी हुन्छन्।
सामान्य उत्पादन:
ग्राइन्डिङ डिस्कहरूले विभिन्न उत्पादन प्रक्रियाहरूमा प्रयोगहरू पाउँछन् जहाँ सटीक सामग्री हटाउन आवश्यक हुन्छ, जसले उच्च-गुणस्तरका कम्पोनेन्टहरूको उत्पादनमा योगदान पुर्याउँछ।
ग. सामना गर्नुपर्ने सामान्य समस्याहरू
डिस्कको पहिरन र घर्षण:
निरन्तर प्रयोग गर्नाले ग्राइन्डिङ डिस्कको झर्ने र घर्षण हुन सक्छ, जसले गर्दा यसको कार्यसम्पादनमा असर पर्छ। दक्षता कायम राख्न नियमित निरीक्षण र प्रतिस्थापन आवश्यक छ।
अत्यधिक तातो हुनु:
लामो समयसम्म प्रयोग गर्दा अत्यधिक घर्षणले अत्यधिक तातो हुन सक्छ, जसले डिस्कको स्थायित्व र समाप्त सतहको गुणस्तरलाई असर गर्छ। उचित शीतलन उपायहरू र आवधिक ब्रेकहरू आवश्यक छन्।
अवरुद्ध:
डिस्कहरू पिस्दा सामग्रीको अवशेष जम्मा हुन सक्छ, जसले गर्दा तिनीहरूको प्रभावकारिता कम हुन्छ। नियमित रूपमा सफा गर्नाले वा एन्टी-क्लोगिङ सुविधाहरू भएका डिस्कहरू छनौट गर्नाले यो समस्यालाई रोक्न मद्दत गर्छ।
कम्पन र हल्लिने:
असन्तुलन वा असमान घिसारले कम्पन वा डगमगाउन सक्छ, जसले गर्दा फिनिशको गुणस्तर र सञ्चालनको सुरक्षा दुवैमा असर पर्छ। उचित स्थापना र सन्तुलन महत्त्वपूर्ण छ।
गलत डिस्क चयन:
कुनै विशेष सामग्री वा प्रयोगको लागि गलत प्रकारको ग्राइन्डिङ डिस्क छनौट गर्दा अक्षमता र सम्भावित क्षति हुन सक्छ। सामग्री अनुकूलताको आधारमा उचित चयन आवश्यक छ।
यी उपकरणहरूमा भर पर्ने उद्योगहरूको लागि ग्राइन्डिङ डिस्कसँग सम्बन्धित परिभाषा, महत्त्व र सम्भावित चुनौतीहरू बुझ्नु आवश्यक छ। सामान्य समस्याहरूलाई सम्बोधन गरेर र उचित प्रयोग सुनिश्चित गरेर, उद्योगहरूले आ-आफ्नो अनुप्रयोगहरूमा ग्राइन्डिङ डिस्कको प्रभावकारितालाई अधिकतम बनाउन सक्छन्।
ग्राइन्डिङ डिस्कहरूमा झर्ने र च्यात्ने
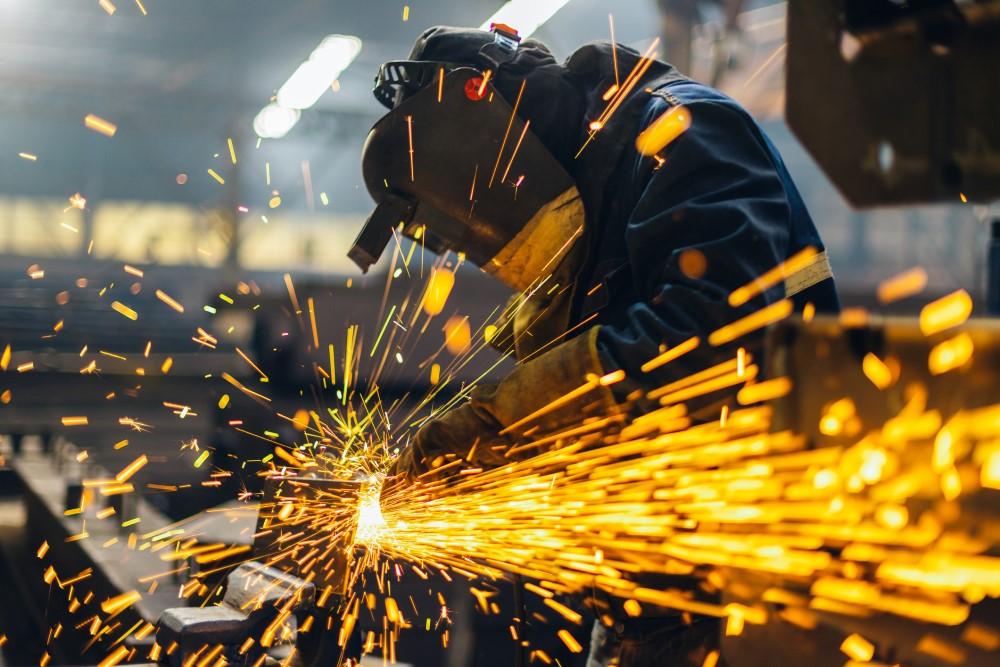
ग्राइन्डिङ डिस्कहरू विभिन्न उद्योगहरूमा आवश्यक उपकरणहरू हुन्, जसले धातु निर्माणदेखि कंक्रीट पालिस गर्ने कार्यहरूको लागि आवश्यक घर्षण प्रदान गर्दछ। ग्राइन्डिङ डिस्कहरूमा झर्ने र च्यात्ने कारणहरू बुझ्नु तिनीहरूको कार्यसम्पादनलाई अनुकूलन गर्न र सुरक्षा सुनिश्चित गर्न महत्त्वपूर्ण छ।
सामग्रीको कठोरता र संरचना:
कठोरता भिन्नता:ग्राइन्डिङ डिस्कहरूमा फरक-फरक कठोरता स्तर भएका सामग्रीहरू भेटिन्छन्। धातु र कंक्रीट जस्ता घर्षण गर्ने सामग्रीहरू कठोरतामा उल्लेखनीय रूपमा फरक हुन सक्छन्। कडा सामग्रीहरू विरुद्ध निरन्तर ग्राइन्डिङ गर्नाले घिसार्ने प्रक्रिया तीव्र हुन्छ।
सामग्री संरचना:ग्राइन्डिङ डिस्कमा घर्षण तत्वहरूको उपस्थितिले ग्राइन्डिङ डिस्कको घिसारलाई असर गर्न सक्छ। घर्षण कणहरूले डिस्कको घिसारलाई तीव्र बनाउन सक्छ।
ग्राइन्डिङ प्रेसर र बल:
अत्यधिक चाप:ग्राइन्डिङ डिस्कमा अत्यधिक दबाब दिनाले छिटो बिग्रन सक्छ। डिस्कमा अनावश्यक दबाबबाट बच्नको लागि विशेष प्रयोगको लागि सिफारिस गरिएको दबाब प्रयोग गर्नु आवश्यक छ।
अपर्याप्त बल: अर्कोतर्फ, अपर्याप्त बलको कारणले गर्दा लामो समयसम्म पिस्न सक्छ, जसले गर्दा थप घर्षण र ताप उत्पन्न हुन्छ, जसले गर्दा घिस्रन पनि हुन सक्छ।
डिस्क गुणस्तर र संरचना:
घर्षण सामग्रीको गुणस्तर:ग्राइन्डिङ डिस्कमा प्रयोग हुने घर्षण सामग्रीको गुणस्तरले यसको आयुमा उल्लेखनीय प्रभाव पार्छ। उच्च-गुणस्तरको घर्षण सामग्रीहरूले पहिरन प्रतिरोध गर्छन् र लामो समयसम्म तीखोपन कायम राख्छन्।
बन्धन एजेन्ट:घर्षण कणहरूलाई एकसाथ राख्ने बन्डिङ एजेन्टले महत्त्वपूर्ण भूमिका खेल्छ। राम्रोसँग डिजाइन गरिएको बन्डिङ एजेन्टले डिस्कको टिकाउपन बढाउँछ।
कार्य वातावरण अवस्थाहरू:
तापक्रम:ग्राइन्डिङ गर्दा उत्पन्न हुने उच्च तापक्रमले डिस्कको संरचनालाई असर गर्न सक्छ। अत्यधिक गर्मीले बन्डिङ एजेन्टलाई कमजोर बनाउँछ र घिस्रने गति बढाउँछ।
आर्द्रता र प्रदूषकहरू:कार्य वातावरणमा ओसिलोपन वा दूषित पदार्थहरूको सम्पर्कले ग्राइन्डिङ डिस्कको अखण्डतालाई असर गर्न सक्छ, जसले गर्दा छिटो पहिरन हुन्छ।
अपरेटर प्रविधि:
उचित प्रविधि:अपरेटर सीप र प्रविधि महत्त्वपूर्ण छन्। गलत कोणमा पीस्ने वा अत्यधिक बल प्रयोग गर्ने जस्ता अनुचित प्रयोगले असमान घिसारमा योगदान पुर्याउन सक्छ र डिस्कको आयु घटाउन सक्छ।
नियमित निरीक्षण:सञ्चालकहरूले ग्राइन्डिङ डिस्कमा क्षति वा जीर्णताको कुनै पनि संकेतको लागि नियमित रूपमा निरीक्षण गर्नुपर्छ। निश्चित बिन्दुभन्दा बढी जीर्णता देखाउने डिस्कहरू तुरुन्तै बदल्नुपर्छ।
डिस्क साइज र RPM अनुकूलता:
सही आकार निर्धारण:ग्राइन्डरको लागि सही डिस्क साइज प्रयोग गर्नु महत्त्वपूर्ण छ। गलत आकारको डिस्कले असमान रूपमा लगाउन सक्छ वा सुरक्षा जोखिम निम्त्याउन सक्छ।
RPM अनुकूलता:ग्राइन्डिङ डिस्कको लागि सिफारिस गरिएको रिभोलुसन प्रति मिनेट (RPM) पालना गर्नाले इष्टतम कार्यसम्पादन सुनिश्चित हुन्छ र समयपूर्व झर्ने समस्याबाट बचाउँछ।
नियमित मर्मतसम्भार, सिफारिस गरिएका सञ्चालन अवस्थाहरूको पालना, र कार्यको लागि सही ग्राइन्डिङ डिस्क छनौट गर्नु भनेको घिसार्ने र च्यात्ने कामलाई कम गर्न आवश्यक अभ्यासहरू हुन्। घिसार्ने कामलाई असर गर्ने कारकहरू बुझेर, अपरेटरहरूले ग्राइन्डिङ डिस्कहरूको दीर्घायु र दक्षता बढाउन सक्छन्, जसले सुरक्षित र अधिक उत्पादक ग्राइन्डिङ सञ्चालनमा योगदान पुर्याउँछ।
असमान पिसाइ
असमान ग्राइन्डिङ भन्नाले त्यस्तो अवस्थालाई बुझाउँछ जहाँ ग्राइन्डिङ गर्दा सतह एकरूप र सहज रूपमा समाप्त हुँदैन। यो समस्या विभिन्न कारणले उत्पन्न हुन सक्छ र वर्कपीसको गुणस्तरमा असर पार्न सक्छ। असमान ग्राइन्डिङमा योगदान गर्ने सामान्य कारकहरू र सम्भावित समाधानहरू यहाँ दिइएका छन्:
गलत ग्राइन्डिङ ह्वील चयन:
समाधान:ग्राइन्डिङ ह्वील ग्राइन्डिङ गरिएको सामग्रीको लागि उपयुक्त छ भनी सुनिश्चित गर्नुहोस्। विभिन्न सामग्रीहरूलाई विशिष्ट घर्षण गुणहरू चाहिन्छ। प्रयोगको लागि सही ह्वील प्रकार, ग्रिट साइज, र बन्ड छनौट गर्नुहोस्।
अनुचित पाङ्ग्रा ड्रेसिङ:
कारण:राम्रोसँग नबनाइएको ग्राइन्डिङ ह्वीलले असमान घिसार्ने र अप्रभावी काट्ने समस्या निम्त्याउन सक्छ।
समाधान:ग्राइन्डिङ ह्वीलको आकार कायम राख्न र जम्मा भएका फोहोरहरू हटाउन नियमित रूपमा ड्रेसिङ गर्नुहोस्। उचित ड्रेसिङले एकरूप काट्ने सतह सुनिश्चित गर्दछ।
अपर्याप्त ग्राइन्डिङ फ्लुइड वा शीतलक:
कारण:पिस्ने तरल पदार्थको अपर्याप्त वा अनुचित प्रयोगले घर्षण र ताप बढाउन सक्छ, जसले गर्दा असमान पिस्ने हुन्छ।
समाधान:ताप घटाउन र घर्षण कम गर्न उपयुक्त ग्राइन्डिङ फ्लुइड वा शीतलक प्रयोग गर्नुहोस्। एकरूप परिणाम प्राप्त गर्न उचित शीतलक आवश्यक छ।
गलत ग्राइन्डिङ प्यारामिटरहरू:
कारण:अत्यधिक गति, फिड दर, वा काट्ने गहिराइ जस्ता गलत ग्राइन्डिङ प्यारामिटरहरू प्रयोग गर्नाले असमान ग्राइन्डिङ हुन सक्छ।
समाधान:सामग्री र अनुप्रयोग आवश्यकताहरू अनुसार ग्राइन्डिङ प्यारामिटरहरू समायोजन गर्नुहोस्। इष्टतम सेटिङहरूको लागि निर्माता सिफारिसहरू हेर्नुहोस्।
जीर्ण ग्राइन्डिङ ह्वील:
कारण:जीर्ण ग्राइन्डिङ ह्वीलले एकरूप काट्ने सतह प्रदान नगर्न सक्छ, जसले गर्दा असमान ग्राइन्डिङ हुन्छ।
समाधान:ग्राइन्डिङ ह्वील यसको प्रयोगयोग्य आयुको अन्त्यमा पुगेपछि बदल्नुहोस्। घिसिएको संकेतहरूको लागि नियमित रूपमा पाङ्ग्रा निरीक्षण गर्नुहोस्।
असमान चाप वा फिड दर:
कारण:ग्राइन्डिङको समयमा असमान दबाब वा असंगत फिड दरहरूले सामग्री अनियमित रूपमा हटाउन सक्छ।
समाधान:वर्कपीसमा एकरूप दबाब दिनुहोस् र एकरूप फिड दर कायम राख्नुहोस्। अपरेटरको सीप र विवरणमा ध्यान दिनु महत्त्वपूर्ण छ।
मेसिन समस्याहरू:
कारण:ग्राइन्डिङ मेसिनमा हुने यान्त्रिक समस्याहरू, जस्तै गलत अलाइनमेन्ट वा स्पिन्डलमा समस्याहरूले गर्दा असमान ग्राइन्डिङ हुन सक्छ।
समाधान:ग्राइन्डिङ मेसिनको नियमित मर्मतसम्भार जाँच गर्नुहोस्। उचित कार्यक्षमता सुनिश्चित गर्न कुनै पनि मेकानिकल समस्याहरूलाई तुरुन्तै सम्बोधन गर्नुहोस्।
वर्कपीस फिक्स्चरिङ:
कारण:राम्रोसँग सुरक्षित नभएको वा गलत तरिकाले मिलाइएको वर्कपीसले असमान पीस्ने समस्या निम्त्याउन सक्छ।
समाधान:वर्कपीसको उचित फिक्स्चरिङ र पङ्क्तिबद्धता सुनिश्चित गर्नुहोस्। ग्राइन्डिङ प्रक्रियाको क्रममा चल्नबाट रोक्नको लागि यसलाई कडा रूपमा सुरक्षित गर्नुहोस्।
असमान ग्राइन्डिङलाई सम्बोधन गर्न उचित उपकरण सेटअप, सही सञ्चालन प्यारामिटरहरू, र नियमित मर्मत अभ्यासहरूको संयोजन आवश्यक पर्दछ। ग्राइन्डिङ अनुप्रयोगहरूमा उच्च-गुणस्तर र सुसंगत परिणामहरू प्राप्त गर्न समस्याहरू तुरुन्तै पहिचान गर्न र सुधार गर्न अपरेटरहरूलाई तालिम दिइनुपर्छ। नियमित निरीक्षण र उत्कृष्ट अभ्यासहरूको पालनाले ग्राइन्डिङ प्रक्रियाको क्रममा कुशल र एकरूप सामग्री हटाउन योगदान पुर्याउँछ।
अत्यधिक तताउने समस्याहरू
ग्राइन्डिङको समयमा अत्यधिक तातो हुनु एउटा सामान्य समस्या हो जसले ग्राइन्डिङ ह्वील र वर्कपीस दुवैको कार्यसम्पादनलाई असर गर्न सक्छ। अत्यधिक गर्मीले पाङ्ग्राको आयु घटाउने, वर्कपीसमा थर्मल क्षति हुने र समग्रमा घट्दो ग्राइन्डिङ दक्षता सहित विभिन्न समस्याहरू निम्त्याउन सक्छ। अत्यधिक तातो हुने समस्याहरूलाई सम्बोधन गर्ने सम्भावित कारणहरू र समाधानहरू यहाँ दिइएका छन्:
गलत ग्राइन्डिङ प्यारामिटरहरू:
कारण:अत्यधिक गति, फिड दर, वा काट्ने गहिराइ जस्ता अनुचित ग्राइन्डिङ प्यारामिटरहरू प्रयोग गर्नाले अत्यधिक ताप उत्पन्न हुन सक्छ।
समाधान:सिफारिस गरिएको दायरा भित्र ग्राइन्डिङ प्यारामिटरहरू समायोजन गर्नुहोस्। ग्राइन्डिङ गरिएको सामग्रीको आधारमा इष्टतम सेटिङहरूको लागि निर्माताको दिशानिर्देशहरू हेर्नुहोस्।
अपर्याप्त शीतलन वा स्नेहन:
कारण:शीतलक वा ग्राइन्डिङ फ्लुइडको अपर्याप्त प्रयोगले घर्षण र गर्मी बढ्न सक्छ।
समाधान:ग्राइन्डिङ प्रक्रियाको क्रममा पर्याप्त मात्रामा शीतलक वा लुब्रिकेन्टको आपूर्ति सुनिश्चित गर्नुहोस्। उचित शीतलनले तापलाई नष्ट गर्न मद्दत गर्दछ र थर्मल क्षतिलाई रोक्छ।
गलत पाङ्ग्रा चयन:
कारण:ग्राइन्डिङ ह्वील छनोट गर्दा सामग्री पिस्ने क्रममा अनुपयुक्त स्पेसिफिकेसनहरू हुन सक्छन्।
समाधान:विशेष प्रयोगको लागि सही घर्षण प्रकार, ग्रिट साइज, र बन्ड भएको ग्राइन्डिङ ह्वील छान्नुहोस्। सामग्रीसँग पाङ्ग्रा मिलाउँदा गर्मी उत्पादन कम हुन्छ।
वर्कपीस सामग्री समस्याहरू:
कारण:केही सामग्रीहरू, विशेष गरी कम थर्मल चालकता भएकाहरू, ग्राइन्डिङको समयमा अत्यधिक तातो हुने सम्भावना बढी हुन्छ।
समाधान:कम थर्मल चालकता भएका सामग्रीहरूको लागि ग्राइन्डिङ प्यारामिटरहरू समायोजन गर्नुहोस्। ताप-संवेदनशील सामग्रीहरूको लागि डिजाइन गरिएको विशेष ग्राइन्डिङ व्हील प्रयोग गर्ने विचार गर्नुहोस्।
पाङ्ग्राको ड्रेसिङ समस्याहरू:
कारण:ग्राइन्डिङ ह्वीलको अनियमितता वा अनुचित ड्रेसिङले असमान सम्पर्क र गर्मी निर्माण हुन सक्छ।
समाधान:ग्राइन्डिङ ह्वीललाई यसको आकार कायम राख्न र कुनै पनि ग्लेजिङ वा जम्मा भएको फोहोर हटाउन नियमित रूपमा ड्रेसिङ गर्नुहोस्। राम्रोसँग ड्रेसिङ गरिएका पाङ्ग्राहरूले ग्राइन्डिङको निरन्तर प्रदर्शन सुनिश्चित गर्छन्।
अपर्याप्त मेसिन मर्मतसम्भार:
कारण:राम्रोसँग मर्मत नगरिएका ग्राइन्डिङ मेसिनहरूले अत्यधिक तातो हुने समस्या निम्त्याउन सक्छन्।
समाधान:ग्राइन्डिङ मेसिनको नियमित मर्मतसम्भार गर्नुहोस्, जसमा शीतलक प्रणालीहरू जाँच गर्ने, पाङ्ग्रा ड्रेसिङ उपकरणहरूको निरीक्षण गर्ने र उचित पङ्क्तिबद्धता सुनिश्चित गर्ने समावेश छ। कुनै पनि मेकानिकल समस्याहरूलाई तुरुन्तै सम्बोधन गर्नुहोस्।
अपर्याप्त पाङ्ग्रा शीतलक प्रवाह:
कारण:ग्राइन्डिङ क्षेत्रमा अपर्याप्त शीतलक प्रवाहले तापको अपव्यय कम गर्न सक्छ।
समाधान:शीतलक वितरण प्रणाली जाँच गर्नुहोस् र अनुकूलन गर्नुहोस्। शीतलक दक्षता कायम राख्न शीतलक प्रभावकारी रूपमा ग्राइन्डिङ जोनमा पुग्छ भनी सुनिश्चित गर्नुहोस्।
अत्यधिक पिस्ने समय:
कारण:लामो समयसम्म ब्रेक बिना पिस्ने सत्रहरूले गर्मी निर्माणमा योगदान पुर्याउन सक्छ।
समाधान:अत्यधिक गर्मी जम्मा हुनबाट रोक्नको लागि बीच-बीचमा ग्राइन्डिङ लागू गर्नुहोस् र ब्रेक दिनुहोस्। यो दृष्टिकोण विशेष गरी ठूला वा चुनौतीपूर्ण ग्राइन्डिङ कार्यहरूको लागि महत्त्वपूर्ण छ।
ग्राइन्डिङमा अत्यधिक तातो हुने समस्याहरूलाई सम्बोधन गर्न उचित उपकरण सेटअप, उपयुक्त ग्राइन्डिङ प्यारामिटरहरू, र नियमित मर्मतसम्भार अभ्यासहरू समावेश गर्ने व्यापक दृष्टिकोण आवश्यक पर्दछ। इष्टतम कार्यसम्पादन, विस्तारित उपकरण जीवन, र उच्च-गुणस्तर परिणामहरू सुनिश्चित गर्न अपरेटरहरूले ग्राइन्डिङ प्रक्रियाको क्रममा ताप उत्पादनको निगरानी र नियन्त्रण गर्नुपर्छ।
कम्पन सम्बन्धी चिन्ताहरू
ग्राइन्डिङ सञ्चालनको क्रममा अत्यधिक कम्पनले विभिन्न समस्याहरू निम्त्याउन सक्छ, जसमा सतहको गुणस्तरमा कमी, उपकरणको घिसार बढ्नु र ग्राइन्डिङ मेसिनमा सम्भावित क्षति समावेश छ। सटीक र कुशल ग्राइन्डिङ प्रक्रियाहरू प्राप्त गर्न कम्पन चिन्ताहरूलाई सम्बोधन गर्नु महत्त्वपूर्ण छ। कम्पन समस्याहरूलाई कम गर्ने सम्भावित कारणहरू र समाधानहरू यहाँ छन्:
असमान पाङ्ग्राको पहिरन:
कारण:ग्राइन्डिङ ह्वीलमा अनियमित घिसारले वर्कपीससँग असमान सम्पर्क निम्त्याउन सक्छ, जसले गर्दा कम्पन हुन सक्छ।
समाधान:नियमित रूपमा ग्राइन्डिङ ह्वीलको निरीक्षण गर्नुहोस् र सतहलाई एकरूप र समतल राख्न लगाउनुहोस्। उचित ह्वील मर्मतसम्भारले कम्पन कम गर्न मद्दत गर्छ।
असंतुलित ग्राइन्डिङ ह्वील:
कारण:ग्राइन्डिङ ह्वीलमा असन्तुलन, चाहे असमान पहिरन वा निर्माण दोषहरूको कारणले होस्, कम्पन हुन सक्छ।
समाधान:ह्वील ब्यालेन्सर प्रयोग गरेर ग्राइन्डिङ ह्वीललाई सन्तुलनमा राख्नुहोस्। सन्तुलनले तौलको समान वितरण सुनिश्चित गर्दछ र सञ्चालनको क्रममा कम्पनहरू कम गर्दछ।
अपर्याप्त मेसिन क्यालिब्रेसन:
कारण:पाङ्ग्राको स्पिन्डल वा वर्कटेबल जस्ता मेसिनका कम्पोनेन्टहरूको कमजोर क्यालिब्रेसन वा गलत अलाइनमेन्टले कम्पन निम्त्याउन सक्छ।
समाधान:उचित कार्यक्षमता सुनिश्चित गर्न मेसिनका कम्पोनेन्टहरू नियमित रूपमा क्यालिब्रेट र पङ्क्तिबद्ध गर्नुहोस्। मेसिन सेटअप र पङ्क्तिबद्धताको लागि निर्माताको दिशानिर्देशहरू पालना गर्नुहोस्।
वर्कपीस असंतुलन:
कारण:असमान वा अनुचित रूपमा सुरक्षित गरिएको वर्कपीसले असंतुलन सिर्जना गर्न सक्छ र कम्पनहरू उत्पन्न गर्न सक्छ।
समाधान:वर्कपीसलाई राम्रोसँग सुरक्षित गर्नुहोस्, यो समान रूपमा राखिएको र क्ल्याम्प गरिएको सुनिश्चित गर्दै। ग्राइन्डिङ प्रक्रिया सुरु गर्नु अघि कुनै पनि असंतुलन समस्याहरूलाई सम्बोधन गर्नुहोस्।
गलत पाङ्ग्रा चयन:
कारण:अनुपयुक्त स्पेसिफिकेशन्स भएको ग्राइन्डिङ ह्वील प्रयोग गर्दा कम्पन हुन सक्छ।
समाधान:ग्राइन्डिङ गर्ने सामग्रीको लागि सही घर्षण प्रकार, ग्रिट साइज र बन्ड भएको ग्राइन्डिङ ह्वील छान्नुहोस्। एप्लिकेसनसँग पाङ्ग्रा मिलाउँदा कम्पन कम हुन्छ।
मेसिनको बिग्रने र च्यातिने समस्या:
कारण:बिग्रिएका वा बिग्रिएका मेसिनका कम्पोनेन्टहरू, जस्तै बेयरिङ वा स्पिन्डलहरूले कम्पनमा योगदान पुर्याउन सक्छन्।
समाधान:नियमित रूपमा जीर्ण मेसिनका पार्टपुर्जाहरूको निरीक्षण र प्रतिस्थापन गर्नुहोस्। उचित मर्मतसम्भारले अत्यधिक कम्पनहरू रोक्न मद्दत गर्दछ र ग्राइन्डिङ मेसिनको आयु बढाउँछ।
अपर्याप्त शीतलक प्रवाह:
कारण:ग्राइन्डिङ क्षेत्रमा अपर्याप्त शीतलक प्रवाहले ताप निर्माण र कम्पन निम्त्याउन सक्छ।
समाधान:उचित शीतलन सुनिश्चित गर्न शीतलक वितरण प्रणालीलाई अनुकूलन गर्नुहोस्। प्रभावकारी शीतलनले थर्मल विस्तार र संकुचन हुने जोखिम कम गर्छ, जसले कम्पन निम्त्याउन सक्छ।
उपकरण धारक समस्याहरू:
कारण:उपकरण होल्डर वा स्पिन्डल इन्टरफेसमा समस्या हुँदा कम्पन हुन सक्छ।
समाधान:उपकरण होल्डर सुरक्षित रूपमा माउन्ट गरिएको छ र स्पिन्डलसँग राम्रोसँग मिलाइएको छ भनी सुनिश्चित गर्नुहोस्। कम्पनहरू कम गर्न उच्च-गुणस्तर र राम्रोसँग मर्मत गरिएको उपकरण होल्डरहरू प्रयोग गर्नुहोस्।
मेसिनको जग:
कारण:कमजोर मेसिनको जग वा अपर्याप्त समर्थनले कम्पन बढाउन सक्छ।
समाधान:ग्राइन्डिङ मेसिन स्थिर र राम्रोसँग डिजाइन गरिएको जगमा जडान गरिएको छ भनी सुनिश्चित गर्नुहोस्। मेसिनमा प्रसारित कम्पनहरू कम गर्न कुनै पनि संरचनात्मक समस्याहरूलाई सम्बोधन गर्नुहोस्।
ग्राइन्डिङमा कम्पन सम्बन्धी चिन्ताहरूलाई प्रभावकारी रूपमा सम्बोधन गर्न उचित मेसिन मर्मतसम्भार, पाङ्ग्रा चयन, र वर्कपीस ह्यान्डलिङको संयोजन आवश्यक पर्दछ। अपरेटरहरूले समस्याहरू तुरुन्तै पहिचान गर्न र समाधान गर्न नियमित निरीक्षण र मर्मतसम्भार अभ्यासहरू लागू गर्नुपर्छ, जसले गर्दा ग्राइन्डिङ कार्यसम्पादन र गुणस्तरमा सुधार हुन्छ।
ग्राइन्डिङमा लोडिङ समस्याहरू
ग्राइन्डिङमा लोडिङ भन्नाले ग्राइन्डिङ ह्वीलमा रहेको घर्षणकारी दानाहरू बीचको खाली ठाउँहरू ग्राइन्डिङ भएको सामग्रीले भरिएको घटनालाई बुझाउँछ, जसले गर्दा काट्ने कार्य कम हुन्छ र घर्षण बढ्छ। लोडिङले ग्राइन्डिङ प्रक्रियाको दक्षता र गुणस्तरमा नकारात्मक असर पार्न सक्छ। लोडिङ समस्याहरूलाई सम्बोधन गर्ने सम्भावित कारणहरू र समाधानहरू यहाँ दिइएका छन्:
नरम वर्कपीस सामग्री:
कारण:नरम पदार्थहरू पिस्दा घर्षण गर्ने दानाहरू छिटो बन्द हुन सक्छन्।
समाधान:नरम सामग्रीहरूमा काम गर्दा मोटो ग्रिट र खुला संरचना भएको ग्राइन्डिङ ह्वील प्रयोग गर्नुहोस्। यसले छिटो लोड हुनबाट रोक्न मद्दत गर्दछ र कुशलतापूर्वक चिप हटाउन अनुमति दिन्छ।
सामग्री प्रदूषण:
कारण:वर्कपीस सामग्रीमा रहेका दूषित पदार्थहरू, जस्तै तेल, ग्रीस, वा शीतलक अवशेषहरूले लोडिङमा योगदान पुर्याउन सक्छन्।
समाधान:दूषित पदार्थहरू हटाउन पिस्नु अघि वर्कपीसको उचित सफाई सुनिश्चित गर्नुहोस्। लोडिङ कम गर्न उपयुक्त काट्ने तरल पदार्थ वा शीतलक प्रयोग गर्नुहोस्।
गलत शीतलक प्रयोग:
कारण:शीतलकको अपर्याप्त वा अनुचित प्रयोगले अपर्याप्त स्नेहन र शीतलन निम्त्याउन सक्छ, जसको परिणामस्वरूप लोडिङ हुन्छ।
समाधान:शीतलक प्रवाह र सांद्रतालाई अनुकूलन गर्नुहोस्। लोड हुनबाट रोक्न, प्रक्रियालाई लुब्रिकेट र चिसो पार्न शीतलक प्रभावकारी रूपमा ग्राइन्डिङ जोनमा पुग्छ भनी सुनिश्चित गर्नुहोस्।
अपर्याप्त पाङ्ग्राको तीखोपन:
कारण:ढिलो वा जीर्ण ग्राइन्डिङ पाङ्ग्राहरू लोड हुने सम्भावना बढी हुन्छ किनभने तिनीहरूले आफ्नो काट्ने क्षमता गुमाउँछन्।
समाधान:पिस्ने चक्काको तीखोपन कायम राख्न नियमित रूपमा ड्रेसिङ र तिखार्नुहोस्। ताजा घर्षणकारी दानाहरू बाहिर निकाल्न र काट्ने कार्य बढाउन व्हील ड्रेसर प्रयोग गर्नुहोस्।
कम पाङ्ग्रा गति:
कारण:ग्राइन्डिङ ह्वीललाई कम गतिमा सञ्चालन गर्दा चिप्स बाहिर निकाल्न पर्याप्त केन्द्रापसारक बल प्रदान नहुन सक्छ, जसले गर्दा लोडिङ हुन्छ।
समाधान:निश्चित पाङ्ग्रा र वर्कपीस संयोजनको लागि सिफारिस गरिएको गतिमा ग्राइन्डिङ मेसिन सञ्चालन भएको सुनिश्चित गर्नुहोस्। उच्च गतिले राम्रोसँग चिप हटाउन मद्दत गर्न सक्छ।
अत्यधिक चाप:
कारण:पिस्दा धेरै दबाब दिँदा सामग्रीलाई जबरजस्ती पाङ्ग्रामा धकेल्न सकिन्छ, जसले गर्दा लोडिङ हुन सक्छ।
समाधान:मध्यम र एकरूप ग्राइन्डिङ प्रेसर प्रयोग गर्नुहोस्। अत्यधिक दबाब बिना नै चक्का कुशलतापूर्वक काट्नको लागि फिड रेट समायोजन गर्नुहोस् जसले गर्दा लोडिङ हुन्छ।
गलत पाङ्ग्रा विशिष्टताहरू:
कारण:ग्राइन्डिङ ह्वील प्रयोग गर्दा सामग्री ग्राइन्डिङको लागि गलत स्पेसिफिकेसनहरू प्रयोग गर्नाले लोडिङ हुन सक्छ।
समाधान:विशेष प्रयोगको लागि उपयुक्त घर्षण प्रकार, ग्रिट साइज, र बन्ड भएको ग्राइन्डिङ ह्वील छान्नुहोस्। सामग्रीसँग पाङ्ग्रा मिलाउनाले लोड हुनबाट रोक्न मद्दत गर्छ।
अपर्याप्त शीतलक सफाई:
कारण:दूषित वा पुरानो शीतलकले लोडिङ समस्याहरूमा योगदान पुर्याउन सक्छ।
समाधान:दूषित पदार्थ जम्मा हुनबाट रोक्नको लागि नियमित रूपमा शीतलक सफा गर्नुहोस् र बदल्नुहोस्। ताजा र सफा शीतलकले स्नेहन र शीतलक बढाउँछ, लोड हुने सम्भावना कम गर्छ।
अनुचित ड्रेसिङ प्रविधि:
कारण:ग्राइन्डिङ ह्वीलको गलत ड्रेसिङले अनियमितता र लोडिङ निम्त्याउन सक्छ।
समाधान:उपयुक्त ड्रेसिङ उपकरण प्रयोग गरेर पाङ्ग्रालाई राम्रोसँग ड्रेस गर्नुहोस्। लोड हुनबाट रोक्नको लागि पाङ्ग्रा प्रोफाइल एकरूप र अनियमितताबाट मुक्त छ भनी सुनिश्चित गर्नुहोस्।
लोडिङ समस्याहरूलाई प्रभावकारी रूपमा सम्बोधन गर्न उचित पाङ्ग्रा चयन, मेसिन सेटअप, र मर्मत अभ्यासहरूको संयोजन समावेश छ। अपरेटरहरूले सिफारिस गरिएका प्रक्रियाहरू पालना गर्नुपर्छ, उपयुक्त ग्राइन्डिङ प्यारामिटरहरू प्रयोग गर्नुपर्छ, र लोडिङ कम गर्न र ग्राइन्डिङ कार्यसम्पादनलाई अनुकूलन गर्न नियमित पाङ्ग्रा ड्रेसिङ लागू गर्नुपर्छ।
विभिन्न धातु कार्य र निर्माण अनुप्रयोगहरूमा इष्टतम परिणामहरू प्राप्त गर्नको लागि सही ग्राइन्डिङ डिस्क छनौट गर्नु महत्त्वपूर्ण छ। छनोट काम भइरहेको सामग्री, इच्छित फिनिश, र प्रयोग भइरहेको ग्राइन्डरको प्रकार जस्ता कारकहरूमा निर्भर गर्दछ।
सही ग्राइन्डिङ डिस्क छनौट गर्दै
सामग्री अनुकूलता:
लौह धातुहरू (स्टील, फलाम):फेरस धातुहरूको लागि विशेष रूपमा डिजाइन गरिएको ग्राइन्डिङ डिस्कहरू प्रयोग गर्नुहोस्। यी डिस्कहरूमा प्रायः स्टीलको कठोरताको लागि उपयुक्त घर्षणहरू हुन्छन् र लोड हुने सम्भावना कम हुन्छ।
अलौह धातुहरू (एल्युमिनियम, पीतल):नरम धातुहरूको लागि उपयुक्त घर्षण भएका डिस्कहरू छनौट गर्नुहोस् जसले गर्दा धातुहरू जम्मा हुनबाट जोगिन्छन्। एल्युमिनियम अक्साइड वा सिलिकन कार्बाइड डिस्कहरू सामान्य विकल्पहरू हुन्।
घर्षण सामग्री:
एल्युमिनियम अक्साइड:फेरस धातुहरूमा सामान्य-उद्देश्यको पीसको लागि उपयुक्त। यो टिकाउ र बहुमुखी छ।
जिरकोनिया एल्युमिना:फेरस र अलौह धातुहरूमा आक्रामक ग्राइन्डिङको लागि उपयुक्त बनाउने, उच्च काट्ने दक्षता र दीर्घायु प्रदान गर्दछ।
सिलिकन कार्बाइड:अलौह धातु र ढुङ्गा पिस्नको लागि आदर्श। यो एल्युमिनियम अक्साइड भन्दा तिखो तर कम टिकाउ छ।
ग्रिट साइज:
खस्रो ग्रिट (२४-३६):छिटो स्टक हटाउने र भारी-ड्युटी ग्राइन्डिङ।
मध्यम ग्रिट (४०-६०):स्टक हटाउने र सतह समाप्त गर्ने कामलाई सन्तुलनमा राख्छ।
फाइन ग्रिट (८०-१२०):सतह तयारी र हल्का पीस्नको लागि उपयुक्त, चिल्लो फिनिश प्रदान गर्दछ।
पाङ्ग्राको प्रकार:
प्रकार २७ (उदासीन केन्द्र):समतल सतह भएको मानक ग्राइन्डिङ डिस्क, सतह ग्राइन्डिङ र किनाराको कामको लागि आदर्श।
प्रकार २९ (कोनिकल):आक्रामक स्टक हटाउने र राम्रो सतह मिश्रणको लागि कोणात्मक डिजाइन।
प्रकार १ (सीधा):काट्ने अनुप्रयोगहरूको लागि प्रयोग गरिन्छ। यसले सही काट्नेको लागि पातलो प्रोफाइल प्रदान गर्दछ।
आवेदन:
पिस्ने:सामग्री हटाउने र आकार दिने मानक ग्राइन्डिङ डिस्कहरू।
काट्ने:धातु काट्नको लागि कट-अफ पाङ्ग्राहरू प्रयोग गर्नुहोस्, जसले गर्दा सिधा र सफा किनारा प्राप्त हुन्छ।
फ्ल्याप डिस्कहरू:ग्राइन्डिङ र फिनिसिङलाई एउटैमा मिसाउनुहोस्। सतहहरूलाई मिश्रण र चिल्लो बनाउनको लागि उपयुक्त।
ग्राइन्डरसँग अनुकूलता:
ग्राइन्डिङ डिस्क प्रयोग भइरहेको ग्राइन्डरको प्रकार र गतिसँग मिल्दो छ भनी सुनिश्चित गर्नुहोस्। डिस्कको अधिकतम RPM (रिभोलुसन प्रति मिनेट) को लागि निर्माताको सिफारिसहरू जाँच गर्नुहोस्।
कार्य विशिष्टता:
भारी स्टक हटाउने:कुशलतापूर्वक सामग्री हटाउनको लागि मोटो ग्रिट र टाइप २७ वा टाइप २९ डिस्क छनौट गर्नुहोस्।
सतह परिष्करण:चिल्लो फिनिशको लागि फ्ल्याप डिस्कसहितको मध्यम देखि मसिनो ग्रिटहरू छनौट गर्नुहोस्।
सुरक्षा विचारहरू:
सुरक्षा दिशानिर्देशहरू पालना गर्नुहोस्, जसमा सुरक्षा चश्मा र पन्जा जस्ता उपयुक्त व्यक्तिगत सुरक्षात्मक उपकरणहरू (PPE) लगाउने समावेश छ।
थप टिकाउपन र सुरक्षाको लागि प्रबलित डिस्कहरू छनौट गर्नुहोस्।
ब्रान्ड र गुणस्तर:
गुणस्तर र स्थिरताको लागि परिचित प्रतिष्ठित ब्रान्डहरूबाट डिस्कहरू छान्नुहोस्। उच्च-गुणस्तरका डिस्कहरूले राम्रो प्रदर्शन र टिकाउपन प्रदान गर्दछ।
लागत विचार:
ग्राइन्डिङ डिस्कको अपेक्षित आयु र कार्यसम्पादनसँग प्रारम्भिक लागत सन्तुलनमा राख्नुहोस्। उच्च-गुणस्तरका डिस्कहरूको अग्रिम लागत उच्च हुन सक्छ तर समयसँगै राम्रो मूल्य प्रदान गर्न सक्छ।
यी कारकहरूलाई विचार गरेर, अपरेटरहरूले दक्षता, सुरक्षा र इष्टतम परिणामहरू सुनिश्चित गर्दै, आफ्नो विशिष्ट अनुप्रयोगहरूको लागि सही ग्राइन्डिङ डिस्क छनौट गर्न सक्छन्।
निष्कर्ष
निष्कर्षमा, उपयुक्त ग्राइन्डिङ डिस्क छनोट गर्नु सफल धातुकाम र निर्माण परिणामहरू प्राप्त गर्ने एक महत्त्वपूर्ण पक्ष हो। छनोट विभिन्न कारकहरूमा निर्भर गर्दछ जस्तै काम भइरहेको सामग्री, इच्छित फिनिश, र प्रयोगमा रहेको ग्राइन्डरको प्रकार। सामग्री अनुकूलता, घर्षण प्रकार, ग्रिट आकार, पाङ्ग्रा प्रकार, प्रयोग, ग्राइन्डर अनुकूलता, कार्य विशिष्टता, सुरक्षा, ब्रान्ड गुणस्तर, र लागतलाई विचार गरेर, अपरेटरहरूले आफ्नो ग्राइन्डिङ प्रक्रियाहरूमा दक्षता र सुरक्षा बढाउन सूचित निर्णयहरू गर्न सक्छन्।
सुरक्षा दिशानिर्देशहरू पालना गर्नु, उपयुक्त व्यक्तिगत सुरक्षात्मक उपकरणहरू लगाउनु, र ग्राइन्डर र डिस्क अनुकूलताको लागि निर्माता सिफारिसहरू पालना गर्नु आवश्यक छ। चाहे यो भारी स्टक हटाउने, सतह परिष्करण गर्ने, वा काट्ने अनुप्रयोगहरूको लागि होस्, सही ग्राइन्डिंग डिस्कले कामको गुणस्तर र दक्षतामा उल्लेखनीय प्रभाव पार्न सक्छ।
थप रूपमा, घिस्रने र आँसुको लागि आवधिक जाँचहरू, अत्यधिक ताप र कम्पन चिन्ताहरू जस्ता समस्याहरूलाई सम्बोधन गर्ने, र लोडिङ समस्याहरू बुझ्ने कुराहरूले ग्राइन्डिङ डिस्कको आयु लम्ब्याउन र निरन्तर कार्यसम्पादन सुनिश्चित गर्न योगदान पुर्याउँछ।
संक्षेपमा, ग्राइन्डिङ डिस्कहरू छनौट गर्ने, प्रयोग गर्ने र मर्मत गर्ने राम्रोसँग सूचित र व्यवस्थित दृष्टिकोण इष्टतम नतिजाहरू प्राप्त गर्न, उत्पादकता बढाउने र सुरक्षित काम गर्ने वातावरण सुनिश्चित गर्ने महत्वपूर्ण पक्ष हो।
पोस्ट समय: जनवरी-१२-२०२४